The Wood a “friend” of man
A brief history
Men have always been able to use, with more or less advanced techniques, timber as an energy source and as a starting material for the production of goods. The woodwork was one of the first arts of men: the clubs and spears from the dawn of civilization, the canoes carved out of tree trunks, the plows used in agriculture, the three-legged stools to the complex structures of the modern era.
The primitive men used wood to defend themselves, to hunt, to warm up and to erect piles. As time passed men began to develop the waterway, and it is then that the Egyptians and later the Greeks and Romans made use of this material to build boats. Afterwards, during it was during the Middle Ages and Renaissance that wood would become an indispensable means to build furniture and to create beautiful sculptures.
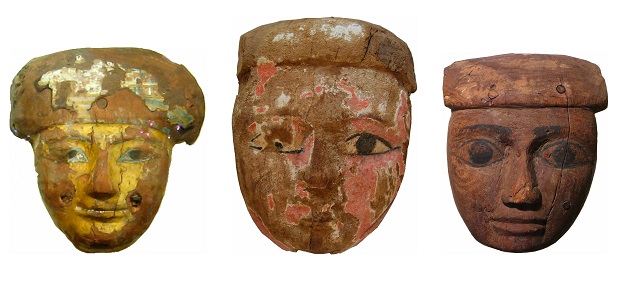
Even today, despite the availability of other materials, wood continues to be used in large quantities in construction, for the construction of furniture and to derive products useful to man, such as paper and all other cellulosic materials.
Since the Middle Ages, after the deforestation, wooden materials became more and more expensive, thus the industry today make greater use of composite materials such as: plywood, chipboard and cartoon-fiber; products that do not deform as easy as natural wood and that do not require a long period of curing.
Before the 50s and 60s there was a carpenter in almost every household, or at least someone who could work with wood. The real carpenter asserted itself after the “boom” of the 60s, a time when they began to increase the number of the workshops/laboratories on a job that, however, was forced to update technologically if they want to keep up with the industry.

After the 60’s in fact a carpenter / craftsman could be seen forced to expand its space by inserting some machines, necessary to carry out his activities and to avoid the risk of closing the shop. Most of them today have set out on the path of modern mechanization; though few, however, have made the leap in the industry.
Characteristics
The perennials are characterized by the presence of plants and branches that grow concentrically outward from year to year and from having the tissues composed mainly of cellulose, hemicellulose and lignin. The wood can have different names, depending on the use to which it is intended:
- Wood if used for fuel
- Wood used for work, construction, if directed to such uses.
The wood is produced by the plant as a structural element, with excellent characteristics of strength and resistance, which is usefully employed by man. As already mentioned, timber is made from cellulose fibers retained by a matrix of lignin; the role of hemicellulose has not yet been clarified.
Once cut, seasoned and dried, the wood is intended for a wide variety of uses:
- Decomposed in fibers it gives rise to the wood pulp, used to produce the paper
- It can be carved and worked with special tools
- It is an important building material since the origins of mankind; when man began to build their own shelters and it still largely used
- It can be used as fuel for heating and cooking
- It is used for the production of the paper, through the production of cellulose pulp, having replaced the cotton industrial era, more rich in cellulose but less abundant and therefore less suited to new production regimes
Wood is commercially classified as “soft” and “hard”. The wood derived from conifers (such as pine or fir) is a tenderer wood; the one from angiosperms (alder, oak, and walnut) is harder. In reality this subdivision can be misleading, since some hardwoods are more tender than those defined tender as for example balsa, while some tender are harder than the tough, for example the rate. In reality this distinction comes from the English nomenclature that defines the conifers “softwood” and the hard angiosperms as “hardwood”, but the translation in softwood and hardwood is a mistake of hypercorrection, since the two words mean simply – and respectively – the coniferous and deciduous.

Different species of wood have different colors, different density and different characteristics of the grain. Because of these differences and the different growth rates, different types of wood have different quality and value. For example, the true mahogany (Swiestenia mahogani), thick and dark, is great for inlays and fine finishes, while the balsa, light, soft, spongy easily hand-cut, is used in the construction of miniature models.
Different types of wood
The solid wood
Wood is a natural and living material. In the trunk, the closest part to the center, is called heartwood, while that more outside is called sapwood. At the center there is the “bone”, which around has rings that indicate the growth of the tree. Each ring corresponds to a year of growth through simply counting one can easily calculate the age of the tree.

After cut with a machine, the trees are brought to the sawmill, where the trunk is sliced according to some well-established patterns. After this, the timber is subjected to seasoning in which it reduces its moisture, and reduces it to acceptable levels for it to work. Normally, the natural drying is the most used, that is, to lay the wooden planks, suitably spaced and protected by a cover, of course, outdoors. After a predetermined period the boards are ready to be processed, but often the moisture level reached happens to be still a bit high for the timber intended for the interior, and thus should be treated artificially.
The processed wood
Among the workable wood the main ones are:
the plywood, the blockboard, particleboard and laminated wood. The plywood is generally made with sheets of poplar or birch, orthogonally disposed between them so as to cancel the forces along the direction of the grain. They are ideal for some structures and may also be of different sizes and thicknesses. Cutting and drilling are not obstacles, but the surfaces may be slightly frayed after the operation: it must therefore always act with sandpaper. The use of screws is not a problem on the flat face of the sheet, while on the thickness, i.e. where you see the various veneers glued, it is not desirable as there is no guarantee for a good seal.

The blockboard is made by two sheets of poplar plywood or birch separated by hard wooden laths adapted to form the structure of the plywood itself. Because of its robustness it is especially recommended for the production of doors, racks and shelves.
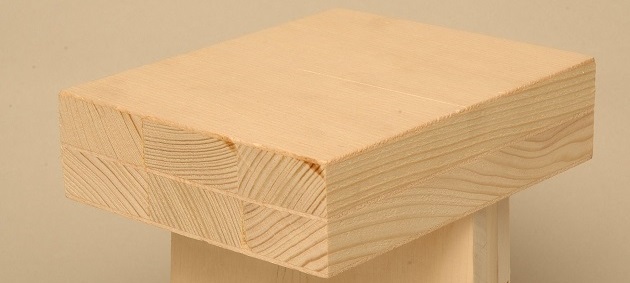
The particleboard (or chipboard) is made up by finely comminuted wood residues, pressed and glued so as to form panels of various sizes and thicknesses. They are used mostly covered with Formica or plastic and often find them in the work plans of modern kitchens or doors of the uprights cabinets, room or modular library lounges. The chipboard is sensitive to moisture and if it gets wet its structure would swell and the surface would crack. The use of nails is not particularly recommended for this material, they usually use special screws similar to those used for iron tapping.
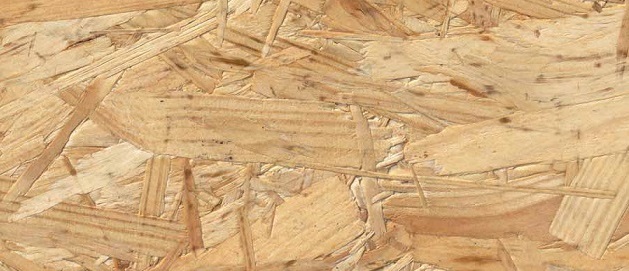
The MDF (Medium Density Fiberboard) is a medium-density fiberboard. It consists of waste remained from wood processing; it’s steam-cured and bonded with thermosetting adhesives. It is therefore an extremely compact material that, unlike the chipboard, can be processed as if it were solid wood, carved and then milled without risking crumbling. It is well suited for the construction of furniture walls, floors and other similar constructions. It is considered an environmentally friendly material because its production does not involve the felling of trees.
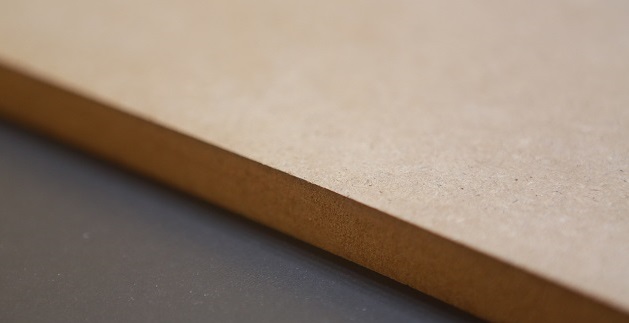
Finally, the laminated wood is made up of strips of solid wood glued together form panels of various sizes and thicknesses. It is robust and lends itself to many uses as tabletops or kitchens, various furniture, shelves of the library etc. Compared to a board of solid wood of the same size in the lamellar panel it offers a much higher strength and deflection. You can find it easily in DIY stores in various sizes.
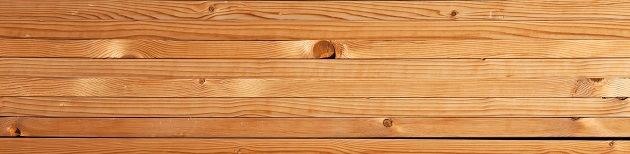
Woodwork in Art History
The use of wood as a building material is very old, as is demonstrated by the huts on stilts in the Neolithic Age. In ancient civilizations (Egypt, Greece, Etruria, Rome) it was spread already in technologically advanced forms. It was always conditioned by the greater or lesser availability of wood material; therefore the major developments in wooden architecture have occurred in the Nordic countries, in Russia, in the East (Japan) and in mountainous areas of the Mediterranean countries.
The applications of the wooden architecture are complex and various, extending from the simple adjunct use for constructions in other materials (scaffolding, frameworks, cover, interior decorations), to the realization of entirely wooden or “mixed” structures or in which the wooden frame has also a supporting function.
The most remarkable aspect of fully wooden constructions lies in the different types of overlay: from simple floor (Egypt, countries with a warm climate) to the truss in its elemental form (from the early Christian to the Romanesque) or in the more complex hull ship (Islamic architecture and Romanesque), the large flat ceilings richly decorated (from the Renaissance to the Baroque, especially in France and England).
Of course the most original and complex use of wood in construction can be traced entirely designed and built in such a material, such as bridges (for example the bridge of Bassano), military and defense works (pillboxes, shelters), triumphal arches or other celebratory apparatuses.
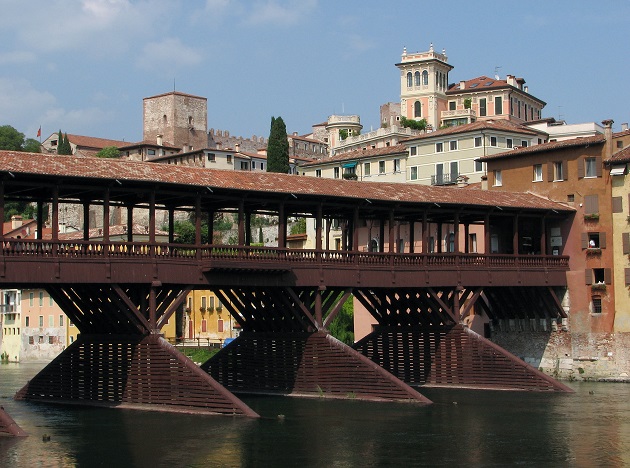
As for the “joint” or “mixed” facilities (brick base, carrying a wooden cage, filled with masonry panels light), they originate from the Middle Ages in Scandinavia, England, Netherlands, France and especially Germany, as predominantly urban typology still imprint themselves in entire districts of German cities.
The use of wood is ancient even in the aspect of sculpture. This, performed through the technique of carving – that is, digging into the material by means of the chisel or chisel – is, in fact present in the classical antiquity of the Western culture. Even though there is no detailed documentation, given the availability of the material, it can be said that Greeks and Romans used the wood for the sacred images. The maximum development of wooden statues came from XI century with the Romanesque and then Gothic architecture, especially in the German regions. Different from the stone, wood in fact allowed for subtle “games of lines” and for plans of figurative cultures, while the use of polychrome accentuated the expressive possibilities. The humanities and the Renaissance brought almost the complete abandonment of polychrome wooden statues, but then it was again used to populate the Sacred Mountains of Piedmont and Lombardy, the Neapolitan cribs and the Spanish altars. In the eighteenth century, finally, the wood was used extensively for statues of saints and angels, often gilded and small size, and in the decoration of houses and buildings.
In addition to architecture and sculpture, the wood was widely used since ancient times for home furnishings and household goods.
Only the dry climate of Egypt, however, has allowed the recovery of a number of wooden objects (furniture, coffins, caskets, boats, etc.) in tombs of the Pharaonic age. The woodwork was also very popular in Islam, and almost all the mosques have their furniture in this material, often finely worked with arabesques, interlacing geometric, etc.; the ivory technique is also spread, bone and mother-pearl, on precious colored woods, such as ebony and teak, even for small objects of private use. But it is especially in the furnishing of every age that this material worked with an extraordinary plethora of forms, variously carved, decorated or even inlaid with precious materials, has always played a key role.
The future of the wood is “secured”
It’s called thermo-vacuum and is an innovative process created by the Institute for the Exploitation of Wood and Tree Species of the National Research Council (CNR-Ivalsa) of San Michele all’Adige (Trento) to produce a new generation of thermally modified wood with high added value and exceptional properties of strength and durability that excludes the use of any chemical substance. The trade mark is registered, the method is covered by three patents, the results have been published in ‘Bio Resources’ and the European Commission funded the project with a record amount.
“The thermo-vacuum drying process combines efficient vacuum energy and heat treatment, with the goal of providing an environmentally friendly product, affordable and of high quality”, says Ottaviano Allegretti, head of the laboratory of Cnr Labess -Ivalsa and part of the scientific project. “With this technology you can provide a timber species such as spruce, dominant in Trentino and in the Alps, the typical characteristics of tropical timber are also imported to this, such a strong aesthetic pleasure and special qualities of durability not found in the natural wood, which makes it particularly suitable for outdoor use, for example in window frames, facades, outdoor furniture and guardrail. The wood provides a very strong competitiveness not only compared to the unprocessed one but also to other materials, plastic and other”.
The method developed by Ivalsa is currently covered by three patents, and “thanks to the reduction of the environmental impact and the cost of long-distance transport and over-exploitation of tropical forests, it produces positive effects on the environment and energy,” says the researcher, “as confirmed by the results recently published in the international journal ‘Bio Resources”.
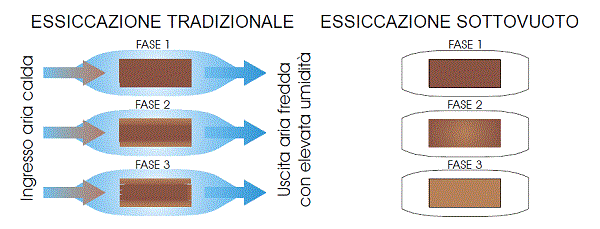
The new process is based on five years of research at the CNR-Ivalsa of San Michele, funded by some private enterprises, by the Autonomous Province of Trento and by the National Research Council. The project was presented as part of the European call for Eco-Innovation by a pool of Italian and French companies together with the Consortium services wood and cork the Swedish Uppsala University and was rated favorable by the European Commission, so as to receive a total amount of 1,8 million euros; the highest ever approved financing for this type of project, because it is considered as “strategic for the high contribution it can make to the environment and to the economy and employment in Italy and Europe,” said Allegretti. “Research now focuses on the certification of the material over its life cycle, from the forest through to disposal, and on the analysis of volatile organic compounds (VOC) that are necessary for the application in the field of interior. The goal is to bring the investments made and the acquired knowledge and technologies to have a real impact in Italian-based Industries “.
Source: CNR Web TV
Craftsmanship and Wood, a centuries old history
Italy has a great tradition and a vast legacy of skilled craftsmen who work with wood to produce mainly tools, furniture and home accessories. Each region has its own history and traditions.
Wood and rock influenced customs and traditions of the Trentino – Alto Adige and stylistically is very similar to that of the Austrian Tyrol. During winter days, the mountain villages remained isolated because of the heavy snowfall that made them inaccessible given the difficulty of traveling on the roads submerged by snow; all this forced the locals to remain isolated in their homes for a long time during the winter. For this reason their daily work was mainly subject to the production of crafts and it characterized the forms needed to cope with the everyday life of self-sustainability. The works were carried out mostly in Tyrolean “workrooms” or “parlors” in home environments covered entirely of wood, where the women worked weaving hand woven on antique looms to then package: pillows, rugs, towels, bedspreads, while men carved wood with great care and attention to make pieces of furniture, ornaments and everyday objects. The wood is also found in the doors of very old house that has an upper lunette and doors carved into rectangular fields, decorated with coats of arms or other figures in relief. But where this craft is truly unsurpassed is the execution of the cradles that today have almost stopped their true function to become genuine decorative objects. We also have to add the production of furniture, characterized by the type of conifer wood, which is decorated with flowers and colorful decorations.

The sculpture of wood, however, is the most widespread form of craftsmanship in Val d’Aosta. With it they create cupboards and carved chests; sabots, typical of Champoluc and the Valle d’Ayas; the chalices and friendship cups; toys and ornaments and household goods.
In Piedmont over time they have developed new artisan products such as musical instruments. In the Cunese we find a thriving production of organs and harps, while in Leinì there are the famous Fourth accordions and woodwind instruments of both wood and metal.
In Liguria we cannot forget the woodwork, art that could not be unknown citizens who for centuries deal with maritime and construction of boats of great impact in the world market. In fact, it is precisely in Genoa that takes place the prestigious international event that has always been able to draw a high number of visitors and create a major impact in terms in Liguria.
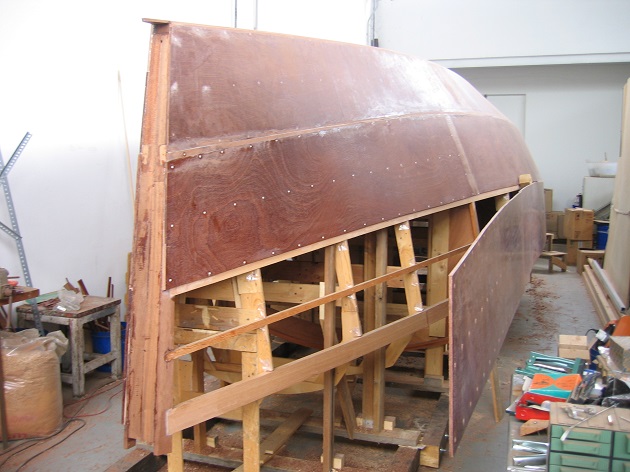
Traditional Abruzzo are the ‘ddu bbotte and cupboards Arischia. The first, built in beech wood, are a kind of concertina still played in village festivals, the latter are cabinets in which to store bread.
In Basilicata the farming and pastoral tradition of the region fully reflects the current production craft enriched by the different cultures of its historic past. Relevant is the production of manufactured wood carvings created by farmers and herdsmen that tell stories of bandits and hunting.
In Puglia wood crafts she has created a flowering of products that include: inlay, carving and the cabinet, which still remains a viable tradition with the contemporary taste always required by the needs of the market. The example of this evolution is the current artists who make paintings inlay large area in addition to the limited extent of their former fellow artists.
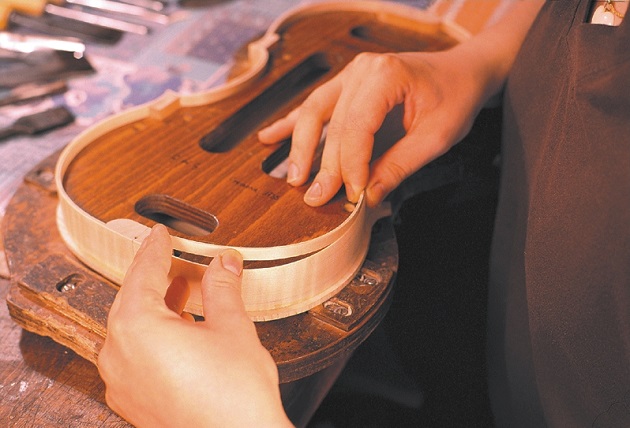
In Calabria the large amount of wood due to the forests of the Sila and Aspromonte, has allowed, since ancient times, a developed wood craftsmanship with lots of forms closely linked to the traditions. One of the most original in the production of wood is called “Art of the Shepherds”, whose work has always remained the same and still uses the technique of hand-carving without the usage of using modern machinery. A characteristic is the production of musical instruments of the highest quality, especially that of luthiers in Bisignano and construction of cane whistles in San Luca and Plati.
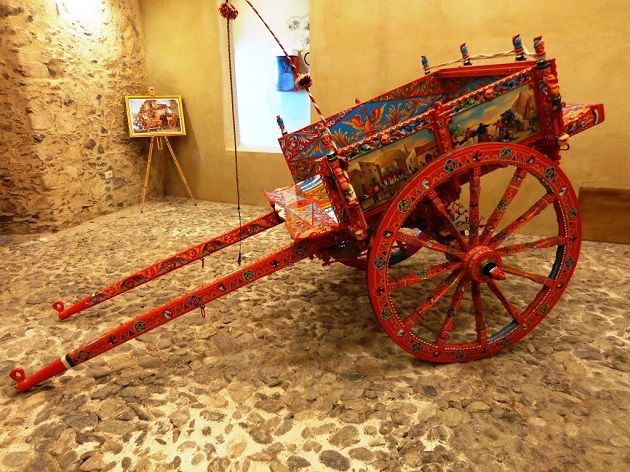
Another region with a great tradition of wood is Sicily with the construction of its symbol: the handcart. Born as a humble means of transport it has become an art form thanks to the carvings and decorations that characterize it. Another expression of ancient artisanship is the “cannalore”, a precious Baroque chandelier with which the workers of Catania pay homage every year in Sant’Agata.
MIDA 2024: the craft fair you can't miss
Lucrezia Piscopo Art, winning project of the Lazio MarteLive 2021 regional final
Interview with Federica Rezzi G, winner of the Lazio MarteLive 2021 final, crafts section
From tradition to today, a special gift for a special professional
The beautiful works of Klimt on the ceramic eggs of La Terra incantata
Valentina Musiu and VALEgnameria, art and craftsmanship in a dynamic and colorful mix